Forward-looking and self-determined
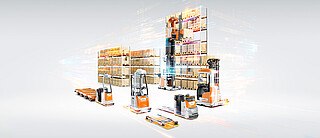
What is autonomy? In intralogistics, it primarily refers to the ability of vehicles to deal with unpredictable situations. A fundamentally different requirement than in classic automation, where devices act independently but in predictable situations.
You can't change reality. Because it looks like this: Only about five per cent of warehouse space is created in newly built halls, on the proverbial "greenfield", where everything can be planned from the outset so that it is ideally tailored to the work processes. Instead, the majority of warehouses are not "greenfield" but "brownfield", i.e. an already existing situation into which new processes have to be integrated. This has consequences, for example, when it comes to automation.
Autonomy differs depending on the sector
Automation is the future - plant managers are convinced of this. STILL ran a survey among its own customers about two years ago, and more than half of them said that they wanted 'more than 60 per cent' of their processes to be automated by 2025, and around a quarter even wanted to automate them completely. Ambitious plans, especially in view of the fact that, at the same time, more than half of the respondents stated that they had not yet automated a single process. However, the answers underline how important the topic is to many and how much they hope to achieve.
Given the expectations, the definition is sometimes blurred: what exactly are automation and autonomy and where are the differences? The question is not trivial because the answer actually depends on the field of application. For the automotive sector, for example, there is a scale that differentiates in levels between "driver does not need feet, vehicle can accelerate and brake on its own" (level 2) or "driver no longer needs to look at the road in certain areas" (level 4). However, to what extent can such a scale be meaningfully applied to autonomous robots in the warehouse, which are faced with completely different challenges than vehicles on the road? The Expert Committee for Autonomous Transport Vehicles of the Association of German Engineers (VDI) made a proposal for sensible criteria at the end of 2021.
It's a matter of centimetres in the warehouse
This includes ten functions that could be used to establish a scale of how autonomously an "Automated Guided Vehicle" (AGV) acts. Can it orient itself independently in an open area? How well does it avoid obstacles? How accurately can it place its load on a shelf? Here it becomes particularly clear what role the industry plays in defining autonomy: In the case of an autonomous car, it is rather secondary whether the vehicle follows a car in front at consistently precise distances - the distances in road traffic are more generous. In intralogistics, however, it is a matter of centimetres, often even millimetres, when, for example, a robot stands in front of a shelf to store or retrieve goods. For an autonomous care robot, on the other hand, it would be crucial that it can communicate with people in need of help. In the warehouse, communication with humans would be a bonus, but not necessarily a prerequisite for autonomous action.
And this is where the "brownfield" comes into play, the reality of warehouses where there are often people walking around, pallets are not in the right place or other imponderables are part of everyday life. Autonomy in such an environment means that an AGV can deal with unpredictable situations in the most anticipatory and self-determined way possible. "A smart robot is constantly aware of its surroundings and adapts its own behaviour according to its findings," says Volker Viereck, Head of intelligent autonomous software development, who, together with his team, is dedicated to the topic of intelligent autonomous robots and is constantly driving this forward. It can work in different ways: A robot can deal with unforeseen situations reactively, i.e. move to the left if there is an obstacle on the right and move to the right if it is getting tight on the left. It can even use all its knowledge to assess which behaviour would be optimal for the current situation and then decide for itself.
If the device plans in advance and implements options
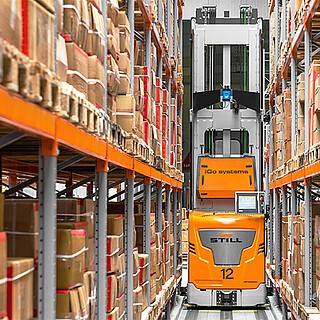
A suitable example would be a forklift truck that can determine without outside help that it has positioned itself a few centimetres too far to the left in front of the shelf in order to pick up its load and then corrects this. "However, it would probably be more efficient if the truck already noticed while approaching that its target was slightly offset and corrected this in advance," explains Harald Bergermann, Head of Solutions Design. He has been working with AGVs for 34 years, at heart always "between innovation and reality", as he says. After all, an autonomous warehouse device cannot simply stop when it encounters an obstacle but can use a variety of information to find the best possible solution as to what should be done. To do this, it should ideally also be able to recognise: Is the obstacle a human being? Is it enough to honk and wait until the person steps aside?
Sensors and software are now at a technical level that facilitates such decisions: trucks recognise their surroundings with the help of various sensors, including 3D cameras, such as the automated MX-X order picking stacker truck from STILL.
"In addition, we are constantly developing AI solutions so that different systems can also coordinate with each other," says Viereck. Together with his team, he already developed the first autonomous vehicle for STILL - the iGo neo order picker, which constantly cooperates with its human companion.
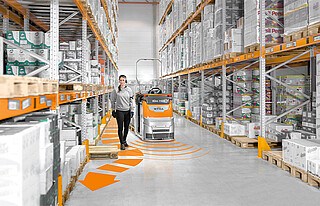
Automation and autonomy each have their strengths
This point is also the decisive difference between autonomy and classic automation, which has shaped processes for a long time: Automated vehicles can move precisely along previously defined routes - but they cannot react to the unexpected. An automated warehouse device that travels through the warehouse following its designated lane is ideally suited for the "greenfield" situations mentioned at the beginning: that is, within environments that are geared to the use of the vehicles in such a way that they can process their orders undisturbed and without unplanned events. In such ideal situations, vehicles with a rather low degree of autonomy can even be more efficient: precisely because autonomous vehicles are intelligent enough to leave their ideal route in case of obstacles - which consequently costs time. "The customer can decide," emphasises Viereck: "Do I want particularly high throughput and idealise my world - or do I need systems that can handle everything, and with no need to spend the money to build a new hall?" This room for manoeuvre is very attractive for many customers, and on top of that, mixed forms are of course also possible.
At the same time, however, customers and manufacturers need to join forces here in order to develop the most attractive applications together. While the automotive industry, with its high unit numbers in the millions, can more easily integrate new functions into costs, intralogistics depend on customers generating clear financial added value with their autonomous vehicles. Both Bergermann and Viereck, however, are convinced that this will very soon become reality. Autonomy is no longer a distant future technology, but already possible. "There is an incredible raison d'être for autonomous robots," says Viereck. "The beginnings are to be found everywhere," adds Bergermann: "With the help of autonomy, completely new economic models will also be established."
Contact request
Subscribe to the Newsletter !
Always up to date with STILL: Subscribe to the STILL newsletter and we will inform you regularly about interesting industry topics.